Foundry Division
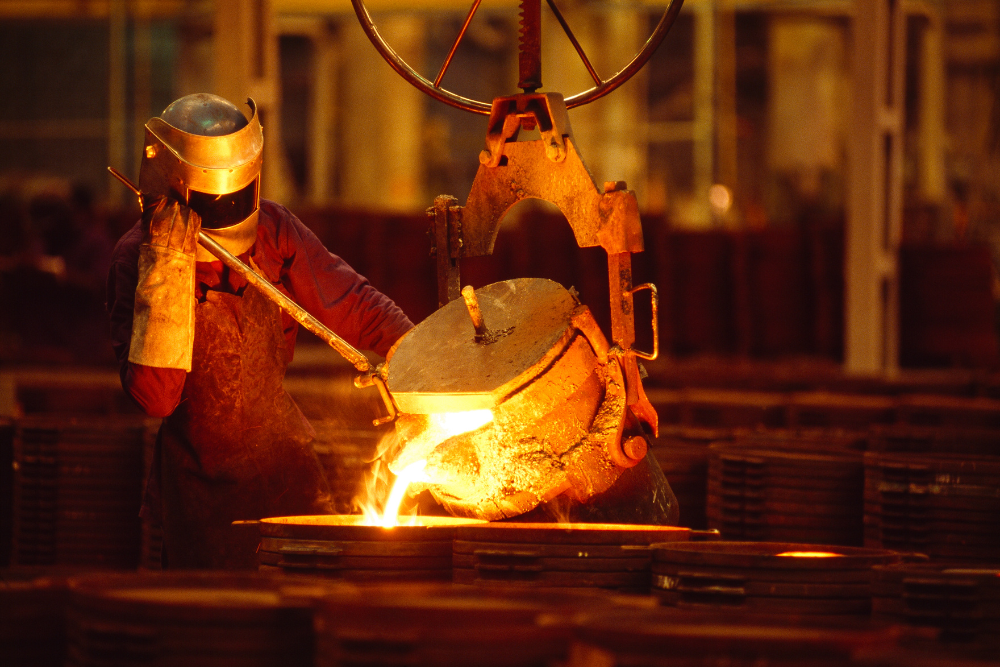
Foundry Machine Facilities
In 2014, we took a significant step forward in our manufacturing capabilities by establishing our in-house Foundry Section at Plant 1. This initiative was driven by our desire to better control the production process and ensure higher quality standards for our castings. Over time, however, the growing demand for our products, coupled with our ongoing commitment to excellence, led us to realize that we needed to expand further.
As a result, we made the strategic decision to open a dedicated Foundry at Plant 2. This new facility is specifically designed to cater to the increasing demand from our customers, providing us with the ability to scale production while maintaining the highest levels of quality.
By separating the foundry operations into its own space, we can focus more on specialized processes, introduce advanced technologies, and streamline operations to meet the ever-growing needs of our clients.
This expansion reflects our commitment to continuous improvement and our dedication to delivering the best possible products to our customers. It also positions us to stay ahead of industry trends and continue growing in an increasingly competitive market.
Foundry Machine Facilities
AVI Oilless Company is well-fitted with modern foundry machine facilities that provide accuracy, efficiency, and reliability in the casting and machining of metals. Our all-inclusive facility meets various industrial needs by providing specific sections to deal with different casting and machining operations. The major sections with their capabilities are listed below:
- Melting Furnace
- Centrifugal Casting
- Continuous Casting
- Miscellaneous
x Maximum Capacity: 500 Kgs
x Advanced melting technology for non-ferrous metals, ensuring consistent temperature control and energy efficiency. Designed for manufacturing high-quality castings with minimal material waste and superior melting precision.
x Maximum Capacity: Outer Diameter (OD) 150 mm to 700 mm
x Ideal for producing cylindrical components with exceptional structural integrity. Our centrifugal casting setup ensures uniform metal distribution and enhanced mechanical properties, suitable for bushings, sleeves, and specialized industrial parts.
x Maximum Capacity: Outer Diameter (OD) 16 mm to 200 mm
x High-precision continuous casting facilities for producing bars, rods, and custom profiles with excellent dimensional accuracy and surface finish. This process ensures minimal porosity and superior material strength.
x Overhead Crane Maximum Capacity: 10 Tons
x Heavy-duty overhead cranes for safe and efficient handling of materials and cast components. Designed to streamline production workflows and accommodate large-scale projects with ease.
Copper Alloy Grades
India Grades: (IS)
- IS: 305-1981 AB-1
- IS: 305-1981 AB-2
- IS: 28-1985 PB-1
- IS: 28-1985 PB-2
- IS: 28-1985 PB-3
- IS: 28-1985
- IS: 318-1981 LTB-3
- IS: 318-1981 LTB-4
USA Grades: (ASTM)
- C63000
- C95200
- C95400
- IS: 28-1985 PB-3
- IS: 28-1985
- IS: 318-1981 LTB-3
- IS: 318-1981 LTB-4
British Standard: (UK)
- BS: 1400 ABI
- BS: 1400 AB2
- BS: 1400 GI
- BS: 1400 PBI
- BS: 1400 PB2
- BS: 1400 LG2
- BS: 1400 LB4
- BS: 1400 LB5
Germany Standard: (DIN)
- CuA110Fe5Ni5
- GCuSn10
- CuSn8
- CuSn12
- GCuSn12Ni
- GCuSn12Pb
- G-SnBz10
- G-SnBz14
- RG-4
- RG-7
- CuZn23A16Mn4Fe3
Centrifugal Casting
Continuous Casting
Sr No. | Description | Maximum Capacity |
---|---|---|
1 | Induction Furnace 1 | 300 Kg |
2 | Induction Furnace 2 | 500 Kg |
3 | Continuous Casting Machine 1 | Ø 30mm to 100mm |
4 | Continuous Casting Machine 2 | Ø 50mm to 250mm |
5 | Continuous Casting Machine 3 | Ø 16mm to 180mm |
6 | Centrifugal Casting Machine 1 | Ø 100mm to 700mm |
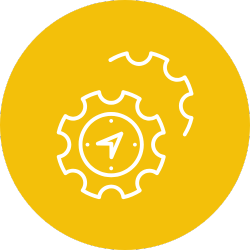
Precision Engineering:
Advanced machinery for accurate and consistent production results.
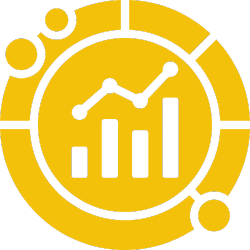
Energy Efficiency:
Designed with modern systems to minimize energy consumption and reduce environmental impact.
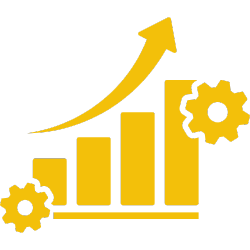
High-Capacity Handling:
Overhead cranes and casting facilities capable of managing large-scale operations.
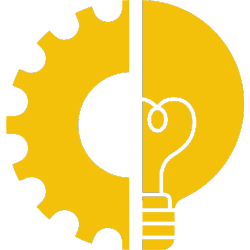
Customizable Solutions:
Facilities tailored to meet diverse client requirements for various casting dimensions and materials.
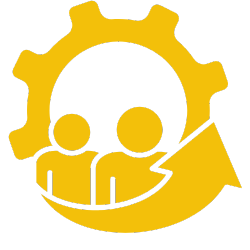
Skilled Workforce:
Operated by experienced professionals ensuring high-quality output and safety.