About us
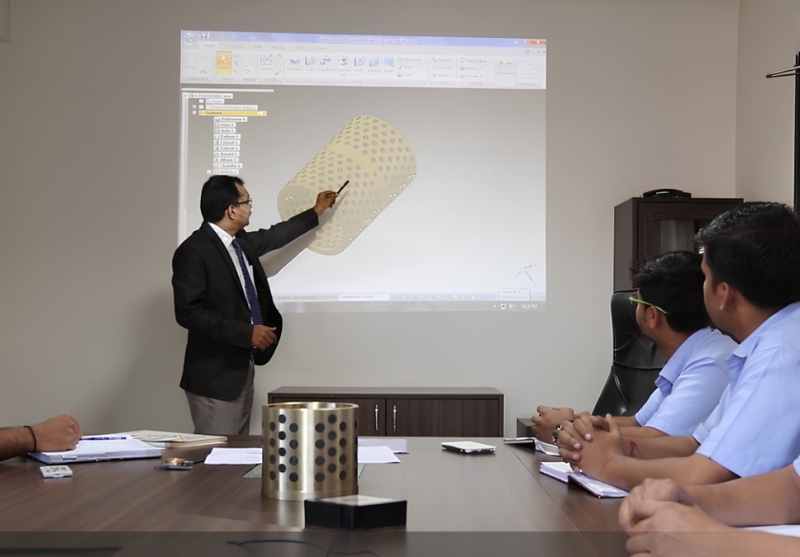
Welcome to Avi Oilless
- Avi Oilless Die Components India Pvt. Ltd. has 30+ years of expertise in the industry.
- Founded by Mr. Moreshwar Hendre, joined by engineer brothers Mr. Pramod and Mr. Prashant.
- Specializes in Non-Ferrous Copper Alloy Castings, Centrifugal Casting, Self-Lubricating Bearings, and Standard Parts for Press Tool Die components.
- Serves industries such as Power, Steel, Rubber & Plastic Processing Machinery, Mining, Defence, and Oil & Gas.
- Focused on providing customized, high-performance solutions to meet international standards.
- Operates Two advanced manufacturing plants: Precision Shop and Foundry.
- Proudly serving over 500+ satisfied customers with superior quality and innovation.
- Dedicated to building long-term partnerships through reliability, excellence, and customer satisfaction.
- Operates Two advanced manufacturing plants: Precision Shop and Foundry.
- Proudly serving over 500+ satisfied customers with superior quality and innovation.
- Dedicated to building long-term partnerships through reliability, excellence, and customer satisfaction.
OUR VISION
To be a global leader in copper alloy casting and self-lubricating products, setting new industry standards through innovation and sustainability.
OUR MISSION
We are committed to optimize customer operations by supplying copper alloy casting and self-lubricating products with reliable, durable solutions and continuously improving quality, performance, and efficiency through research and development.
OUR Goal
Avi Oilless aims to lead the die and mould industry through continuous innovation, high-quality self-lubricating solutions, and expanded global reach. We are committed to sustainability, operational efficiency, and building lasting customer relationships.
Our Journey
1993
Foundation
- AVI Enterprises was established as a proprietary firm specializing in job working, located on the outskirts of Pune, Maharashtra's industrial hub.
1998
Innovation
- Developed proprietary production technology for self-lubricating slide plates and guide bushes, marking a significant step in oilless technology.
1999
First Customer for Self-Lubricating Products
- Bajaj Auto Ltd., India's leading automobile manufacturer, became the first customer for self-lubricating products.
- This partnership focused on creating oilless plates for import substitution, driving advancements in oilless components for Press Dies and Molds.
2000
Production System Established
- A robust production system was implemented for standard components for Press Tools, Dies, and Molds, streamlining operations and improving product quality.
2002
Expansion
- Opened a new plant, AVI Industries, in Uttamnagar, Pune, significantly enhancing production capabilities.
- Obtained ISO 9001:2000 certification, reinforcing the company's commitment to maintaining high-quality standards.
2004
Rebranding
- Rebranded as AVI OILLESS DIE COMPONENTS INDIA PVT. LTD.
- Merged the Uttamnagar plant into the newly formed entity to consolidate operations under the AVI Oilless brand
2005
Product Range Expansion
- Expanded product offerings to include components for Hydropower and Steel Plants, Diversifying into more Industrial sectors.
2006
First Product Catalogue
- Published the first official product catalogue, offering customers a comprehensive overview of the company’s product range.
2007
New Product Development
- Launched self-lubricating bearings designed for Hydropower applications and began supplying to major players like BHEL (Bharat Heavy Electricals Limited).
2008
Capacity Boost
- Established a new plant at Velu (Tal. Bhor, Dist. Pune) to further increase production capacity, supporting growing demand for the company's products.
2013
Recognition and National Expansion
- Honoured with the Indian Leadership Award for Industrial Development by the All-India Achievers Foundation in New Delhi.
2014
Started Foundry Section
- Launched a foundry unit for continuous casting, enabling the production of bars, tubes, and flat products in non-ferrous copper alloys.
- Introduced centrifugal casting facilities, allowing to produce self-lubricating bearings up to 1000mm in diameter.
2017
Award for Innovation
- Received the Star Innovation Award from BHEL Ranipet for excellence in import substitute product development and contribution to the industry.
2018
Further Foundry Expansion
- Enhanced production capacity by adding:
- A continuous casting machine capable of producing products up to 200mm in diameter.
- A centrifugal casting machine capable of producing bearings up to 1000mm in diameter.
- Melting furnaces and a spectrometer for quality checks, ensuring consistent product quality.
2020
Diversified Customer Base
- Expanded the customer base to include industries such as defence, steel, heavy industries, mining, and thermal power, reflecting a broader market presence.
2024
Increased Manufacturing Capabilities
- Significantly boosted manufacturing capacity in both the foundry section and machine shop to meet rising demand.
- Currently serving 500+ clients across various sectors, solidifying its position as a leader in Self-lubricating bushes, non-ferrous castings and standard die components and industrial solutions.